1. Introdução
O projeto do arranjo físico da produção é uma tarefa frequentemente negligenciada na organização do sistema produtivo de uma pequena empresa. No entanto, em empresas industriais de qualquer porte, o layout é determinante para a eficiência do fluxo de produção, gerando impactos para a produtividade e, consequentemente para a redução dos custos de fabricação. O controle de custos, por sua vez, é fundamental para a sobrevivência de novos negócios, o que reforça a importância de ações que contribuam para esta meta.
Além de permitir um melhor aproveitamento de recursos, um bom layout industrial influencia na melhoria física do ambiente de trabalho e na gestão eficiente de todo o processo produtivo. O layout funciona como um "pano de fundo" para a operação do sistema de produção em todos os seus aspectos, interferindo em áreas que vão desde a programação da produção até os sistemas de garantia da qualidade.
Na prática, a estruturação de fábricas de pequeno porte dificilmente é submetida a um estudo detalhado do layout industrial. Geralmente, as fábricas de pequeno porte são originadas de sistemas de produção artesanais que desenvolvem um modelo de organização industrial à medida que o negócio prospera e a demanda aumenta. Uma das consequências disso é que o layout da fábrica tende a ser mais desorganizado, no qual os recursos de produção vão se acomodando no chão-de-fábrica ao passo em que são comprados novos equipamentos para suprir uma demanda crescente. Nesse caso, a racionalidade cede lugar ao empirismo e o uso de técnicas de planejamento de layout fica em segundo plano.
Com objetivo de tratar o projeto de layout de modo racional e planejado, este artigo apresenta um estudo de layout que foi realizado em uma empresa familiar destinada à produção de baterias automotivas em uma fábrica de pequeno porte. Embora a fábrica não apresentasse problemas de layout a ponto de limitar a sua capacidade produtiva atual, constatou-se que o arranjo físico da produção foi projetado somente com base no conhecimento tácito adquirido com a experiência de seus proprietários, sem que houvesse um planejamento formal para sua concepção e implantação. Mesmo que a experiência tenha representado um fator determinante e imprescindível para o projeto do layout atual, a ausência da aplicação de procedimentos formais de análise ainda deixou uma grande margem para melhoria e otimização de fluxos de processos. Essa melhoria provavelmente fará diferença com a concretização do crescimento de demanda que é previsto e, por esse motivo, a empresa tem procurado se antecipar a futuros problemas de layout.
Para a realização do estudo, foi formado um grupo de trabalho que analisou os processos e os fluxos produtivos da fábrica, aplicando técnicas que seguem a metodologia de planejamento sistemático de layout (SLP - Systematic Layout Planning), proposta inicialmente por Muther (1978). A metodologia original de planejamento sistemático de layout tem sido aperfeiçoada ao longo do tempo por autores como Lee (1998) e Kerns (1999). A aplicação relatada neste artigo incorpora esses aperfeiçoamentos, embora a lógica conceitual do sistema SLP permaneça inalterada.
Antes de descrever o processo de aplicação do planejamento sistemático de layout, é necessário entender sua lógica de funcionamento, assim como, os seus pressupostos básicos. Esses assuntos são abordados na segunda seção do artigo. Após essa seção, são apresentados os procedimentos metodológicos do trabalho, que demonstram o delineamento da pesquisa e as técnicas de coleta e análise de dados que foram utilizadas. Em seguida, o texto descreve o estudo de layout, propriamente dito, e seus principais resultados. O artigo se encerra com uma seção de considerações finais que destaca as principais conclusões acerca do trabalho realizado.
2. Planejamento sistemático de layout
O layout das instalações produtivas se preocupa com a disposição física dos recursos de transformação, isto é, máquinas, equipamentos e pessoas (Tompkins et al., 2010). Essa disposição física determina o fluxo do processo e, de acordo com a natureza do processo, o arranjo físico da produção pode se enquadrar dentro de uma das quatro categorias básicas já consolidadas na literatura da área (Garcia-Diaz, Smith, 2008; Villar, Nóbrega Júnior, 2004): layout posicional, layout funcional, layout linear, layout celular.
O projeto do layout funcional geralmente é mais complexo que o dos demais tipos, pois envolve fluxos multidirecionais entre recursos de transformação que são agrupados de acordo com a sua função no processo. De acordo com Heizer e Render (2001), o principal objetivo do layout funcional é minimizar o custo total de movimentação de materiais entre os centros produtivos. Em geral, este custo de movimentação está relacionado a pelo menos três variáveis (fluxo, distância e custo unitário), expressas na seguinte função-objetivo:

em que:
CTM: custo total de movimentação de materiais
n: número total de centros de trabalho do layout
Fij: fluxo entre os centros de trabalho i e j, geralmente medido em carga movimentada ou número de transportes por unidade de tempo
Dij: distância entre os centros de trabalho i e j
Cij: custo unitário por distância percorrida entre os centros de trabalho i e j
Apesar de sua complexidade, o projeto de um layout funcional nem sempre é realizado de forma sistemática, dando lugar à intuição ao invés de uma abordagem estruturada de análise e resolução de problemas (Lee, 1998). Em busca de uma abordagem estruturada, Muther (1978) desenvolveu o Planejamento Sistemático de Layout (SLP - Systematic Layout Planning), uma metodologia completa para o projeto e o reprojeto de layout, especialmente útil para layouts funcionais. Embora seja um método antigo, o sistema SLP ainda apresenta uma grande aplicabilidade nos modernos sistemas de produção e serve de referência para projetos de instalações produtivas e também para pesquisas na área.
De acordo com Muther (1978), o SLP é composto por uma estruturação de fases, um modelo de procedimentos e uma série de convenções para identificação, avaliação e visualização dos elementos e das áreas envolvidos no planejamento.
A estruturação das fases do SLP representa o nível de detalhamento que se deve adotar no projeto do arranjo físico da produção. Esse nível de detalhamento é dividido da seguinte forma:
- Fase I: Localização. Nesta fase deve-se determinar a área geográfica a ser utilizada para o planejamento das instalações do novo layout.
- Fase II: Arranjo físico geral. Representa a organização geral entre as diversas áreas. Nesta fase são definidos os fluxos e as inter-relações entre as áreas, resultando no que se chama de arranjo de blocos (block layout).
- Fase III: Arranjo físico detalhado. No planejamento detalhado é estabelecida a localização relativa das máquinas e equipamentos, assim como toda a infraestrutura física necessária para a produção do produto.
- Fase IV: Implantação. Esta é a fase na qual se executa o que foi planejado anteriormente. De maneira concreta, faz-se aqui a movimentação de maquinário, equipamentos e recursos para a instalação da operação.
Todas as fases são inter-relacionadas entre si, de forma que as saídas da fase anterior sirvam de entradas para a fase seguinte. Entretanto, embora exista uma aparente relação de dependência entre as fases, o escopo do projeto pode ser delimitado em apenas uma ou duas fases, especialmente quando o SLP é aplicado no reprojeto de layouts existentes, que possuem necessidades mais específicas de melhoria. Nesse caso, ainda deve ser mantida a hierarquia das fases, que define a ordem de aplicação quando mais de uma fase é executada.
De um modo geral, pode-se afirmar que a estruturação das fases do SLP demonstra a abrangência deste método, que pode ser destinado ao projeto completo de uma instalação produtiva. Além disso, essas fases são compatíveis com os níveis de análise adotados em outros procedimentos de projeto de layout que derivaram do SLP (Kerns, 1999; Lee, 1998). Por exemplo, o método FacPlan, proposto por Lee (1998), trabalha com cinco níveis de planejamento de espaço: I. Global; II. Supra (que juntamente com o nível global corresponde à Fase I do SLP); III. Macro (que corresponde à Fase II do SLP); III. Micro (que corresponde à Fase III do SLP); e, IV. Submicro (que complementa o SLP original com o projeto do posto de trabalho).
As metodologias de planejamento sistemático de layout pressupõem que o projeto de um arranjo físico deve estar apoiado em três conceitos fundamentais (Muther, 1978; Muther, Wheeler, 2000):
1. Inter-relações – grau relativo de dependência ou proximidade entre as atividades.
2. Espaço – quantidade, tipo e forma ou configuração dos itens a serem posicionados.
3. Ajuste – arranjo de áreas e equipamentos da melhor maneira possível.
Com base nesses três conceitos, o modelo de procedimentos do SLP é constituído pelos seguintes elementos:
- Dados de entrada. Os dados de entrada são as variáveis que devem ser levadas em consideração antes do início da análise do arranjo físico. Além das atividades do processo de produção, os outros dados de entrada são representados pelas letras PQRST, que significam: produto (P), quantidade ou volume de produção (Q), roteiro ou sequência do processo de produção (R), serviços de suporte (S) e tempos envolvidos na produção (T).
- Fluxo de materiais. O fluxo de materiais quase sempre se torna o fator predominante de decisão no projeto do arranjo físico. Devem-se identificar os fluxos através das áreas envolvidas, de acordo com a sequência e a intensidade do deslocamento do material. As principais ferramentas utilizadas nessa etapa são aquelas destinadas à análise do fluxo de processos, tais como: fluxograma, carta de processos múltiplos, carta "de-para", mapofluxograma, etc.
- Inter-relações de atividades. Esta é uma análise mais qualitativa, que procura identificar a importância da proximidade relativa entre as áreas. A ferramenta indicada para essa tarefa é conhecida como carta de interligações preferenciais (ou simplesmente, diagrama de relações), na qual se utiliza a escala A, E, I, O, U, X para indicar a necessidade de proximidade entre os diferentes setores do layout. Cada combinação de pares de setores deve receber uma avaliação, sendo que a letra "A" denota a necessidade prioritária de proximidade, a letra "U" denota uma proximidade não importante e a letra "X" indica que a proximidade não é desejada.
- Diagrama de inter-relações. O diagrama de inter-relações é uma ferramenta que procura integrar o mapeamento do fluxo de materiais com a avaliação das interligações preferenciais. Trata-se de uma representação gráfica na qual os círculos denotam as áreas do layout e as linhas, de diferentes tipos e dimensões, denotam o grau de importância das relações entre essas áreas.
- Espaço necessário. É a determinação do espaço requerido para alocação de máquinas e equipamentos.
- Espaço disponível. É a análise do espaço disponível para a instalação de máquinas e equipamentos.
- Diagrama de inter-relações de espaços. Nesta fase o diagrama de inter-relações é aplicado com o objetivo de gerar um arranjo físico prévio, considerando que o espaço requerido já foi devidamente balanceado com o espaço disponível.
- Considerações de mudanças. Nesta etapa ocorrem os ajustes necessários, levando-se em consideração fatores relativos a tipos de processos, métodos de movimentação de materiais, necessidades de pessoal, etc.
- Limitações práticas. Para analisar a viabilidade dos projetos de layout, cada consideração de mudança que houver deve ser comparada com as limitações práticas referentes a custos, restrições técnicas, segurança, etc.
- Avaliação de alternativas. Ao final do procedimento, os diferentes planos alternativos que forem gerados devem ser avaliados, ponderando seus benefícios e limitações.
De acordo com Muther (1978), o modelo de procedimentos do SLP pode ser aplicado tanto na elaboração do arranjo físico geral quanto na elaboração do arranjo físico detalhado (fases II e III da estrutura do SLP). O mesmo se pode afirmar para o modelo de procedimentos do FacPlan (Lee, 1998), pois ele se aplica tanto no planejamento de macrolayout quanto no planejamento de microlayout. Na verdade, o SLP e o FacPlan são métodos complementares, sendo que o FacPlan contribui com um aprimoramento de algumas etapas e técnicas do SLP. Considerando o que têm em comum, os dois modelos de procedimentos representam roteiros completos para projeto e análise de layouts, tal como ilustra a figura 1.
Figura 1. Metodologias de planejamento sistemático de layout.
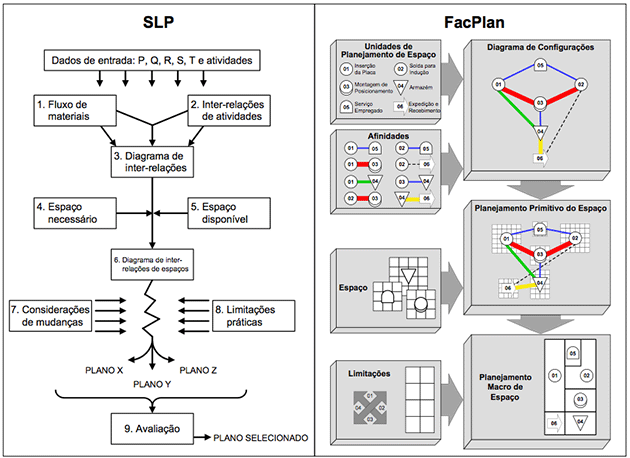
Fonte: Muther (1978) e Lee (1998).
O método FacPlan utiliza a nomenclatura de unidades de planejamento de espaço (UPE's) para identificar as áreas específicas do layout, sejam destinadas a funções produtivas, de armazenagem ou administrativas. Outro ponto a destacar neste método é a análise de afinidades, que integra aspectos quantitativos com qualitativos. No SLP, a análise de afinidades se baseia somente em critérios qualitativos que definem o grau de importância da proximidade relativa entre os diferentes setores do layout por meio da escala A, E, I, O, U, X. Na sequência da aplicação do procedimento SLP, ao elaborar o diagrama de inter-relações (chamado de diagrama de configurações no FacPlan), é necessário observar dois aspetos distintos: a intensidade do fluxo (quantificada normalmente pelo volume de materiais processados) e a necessidade de proximidade (definida qualitativamente na carta de interligações preferenciais). O FacPlan de Lee (1998) integra esses dois aspectos em uma única matriz que combina a intensidade do fluxo com a necessidade de proximidade. Para isso, o método utiliza o conceito de unidade de fluxo equivalente (UFE) que permite, por proporcionalidade, substituir os valores de intensidade de fluxo na carta "de-para" por valores que variam de 0 a 4. Por outro lado, a escala A, E, I, O, U da carta de interligações preferenciais também é substituída por uma escala de 0 a 4 (o "X" é assinalado à parte). A uniformidade de medidas permite construir uma matriz combinada, que une as duas dimensões (quantitativa e qualitativa) por meio da média das duas matrizes anteriores. Essa média é ponderada de acordo com os pesos que se atribuem para os aspectos associados ao fluxo (quantitativos) e para os aspectos não associados ao fluxo (qualitativos).
Devido à sua importância, as metodologias de planejamento sistemático de layout têm sido alvo de diversas pesquisas que procuram adaptá-las a contextos específicos ou sofisticar a aplicação de suas etapas. Por exemplo, Yang et al. (2000) e Tortorella e Fogliatto (2008) buscaram incrementar o sistema SLP com a utilização de ferramentas de apoio à decisão multicritério, em especial o AHP (Analytic Hierarchy Process), refinando a fase de avaliação e seleção de alternativas. Marujo et al. (2010), por sua vez, propuseram a aplicação do SLP em conjunto com técnicas de modelagem da teoria de filas, testando a metodologia proposta em uma oficina de rodas e freios de aeronaves. Já Chien (2004) apresentou conceitos e algoritmos de agrupamento, composição e distância hipotética para alterar os procedimentos e melhorar a praticidade na SLP tradicional. Com uma abordagem alternativa, Djassemi (2007) desenvolveu um procedimento denominado "fluxo de materiais modificado" e o combinou com técnicas do sistema SLP para otimizar o uso do espaço no projeto de layouts industriais.
As pesquisas recentes sobre as metodologias de planejamento sistemático de layout demonstram a atualidade do tema e, principalmente, que a sua aplicação ainda é relevante para diferentes ambientes industriais.
3. Procedimentos metodológicos
Para a aplicação do planejamento sistemático de layout foi formado um grupo de trabalho, que coletou dados do chão-de-fábrica e analisou esses dados para propor melhorias ao layout existente de uma fábrica de baterias automotivas. Do ponto de vista da metodologia científica, o trabalho seguiu a abordagem da pesquisa-ação, na qual os pesquisadores envolveram o objeto pesquisado para o alcance dos objetivos da pesquisa (Coughlan, Coghlan, 2002; Eden, Huxham, 1996). O envolvimento entre os pesquisadores e o objeto pesquisado foi necessário para a aplicação adequada da metodologia, que demandava a participação de pessoas de dentro e de fora da empresa para que a coleta e a análise de dados fossem realizadas com êxito.
O trabalho de campo foi delimitado às áreas produtivas da fábrica, sendo que as áreas administrativas não foram objetos de análise. Quanto ao nível de detalhe do estudo, pode-se afirmar que foi aplicada a parte equivalente à fase II do SLP ou ao nível macro do FacPlan. Nesse caso, o resultado esperado foi o projeto de um arranjo físico geral que define a localização relativa entre as áreas, mas sem alterar a organização de máquinas e equipamentos dentro das áreas produtivas, uma vez que não foram identificados problemas relevantes que justificassem um estudo de microlayout (fase III do SLP).
A aplicação do planejamento sistemático de layout se baseou nas metodologias propostas por Lee (1998) e Muther (1978), que ajudaram a construir um roteiro inicial para a condução do trabalho. O roteiro de partida foi sendo ajustado à medida que as características específicas da fábrica iam sendo analisadas, resultando em uma metodologia que foi aplicada em seis etapas, como descreve o quadro 1.
Quadro 1. Metodologia utilizada.
Etapas |
Atividades |
Técnicas de coleta
de dados |
Ferramentas
de análise |
|
- Desenhar o layout atual
- Caracterizar as áreas que podem ser consideradas como unidades de planejamento de espaço (UPE's)
|
- Análise de documentos da empresa
- Entrevistas informais
- Medição do espaço físico com trena
|
- Planta baixa do layout atual
- Check-list de infraestrutura
|
|
- Selecionar produtos para a análise
- Registrar sequência do processo
- Medir tempos das operações
|
- Observação da rotina
- Cronometragem
- Entrevistas informais
|
- Fluxograma em ramos
- Gráfico de fluxo de processo
- Mapofluxograma
|
|
- Coletar dados de intensidade de fluxo (volume, demanda, movimentações, etc.)
- Montar cartas "de-para"
- Elaborar matrizes de afinidades
|
- Análise de documentos da empresa
- Entrevistas informais
|
- Carta "de-para"
- Matriz de afinidades
|
|
- Elaborar o diagrama de configurações para o layout atual
- Reorganizar configurações alternativas
|
- Análise de documentos da empresa
- Entrevistas informais
|
- Diagrama de configurações
|
- Identificação de necessidades de espaço
|
- Calcular o espaço para as operações atuais e previstas
- Confrontar espaços requeridos com configurações alternativas
|
- Medição do espaço físico com trena
- Entrevistas informais
|
- Planilha de cálculo de espaço
|
- Geração de alternativas e projeto da solução
|
- Projetar layouts alternativos
- Escolher melhor layout
- Projetar layout final
|
- Análise de documentos da empresa
- Entrevistas informais
|
- Plantas baixas de layouts alternativos
|
As seis etapas da metodologia proposta representam uma compilação das boas práticas de projeto de layout. Porém, ao passo que a metodologia proposta procurou capturar boas práticas, ela foi simplificada para se adequar às necessidades de uma fábrica de pequeno porte, mantendo sua facilidade e dinâmica de aplicação.
As etapas da metodologia ilustradas no quadro 1 ocorreram de forma sequencial, com exceção das etapas 4 e 5, que ocorreram em paralelo. Como o estudo era para um layout já existente, a análise de configurações já deveria considerar as limitações do layout para que as possíveis configurações pudessem ser testadas dentro de uma visão mais realista. Já que as posições relativas entre as UPE's (configurações) estavam sujeitas às restrições de espaço do layout atual, as etapas 4 e 5 deveriam ser realizadas de forma integrada. Assim, ao simular diferentes configurações, o espaço necessário estaria definido previamente, de modo que as duas etapas (4 e 5) juntas constituiriam o planejamento primitivo do espaço, segundo a nomenclatura do FacPlan de Lee (1998).
Seguindo a ordem da metodologia de aplicação apresentada no quadro 1, o estudo de layout é descrito na próxima seção.
4. Aplicação
A fábrica estudada pertence a uma empresa familiar e produz baterias automotivas de diferentes modelos. Embora a empresa já tenha mais de 50 anos, a fábrica que foi analisada tem apenas quatro anos de implantação e pode ser considerada como uma instalação que ainda está sujeita aos ajustes necessários para otimizar seu funcionamento na fase inicial de seu ciclo de vida. Devido a um acordo de sigilo, foi decidido que o nome da empresa não seria divulgado neste artigo, omitindo-se todos os dados que pudessem identificar a organização.
As instalações industriais da empresa apresentavam as características típicas de um layout funcional, com um mix diversificado de produtos e com recursos de transformação agrupados de acordo com a sua função no processo produtivo. Embora as sequências dos processos dos diversos tipos de bateria fossem semelhantes, os tempos de fabricação eram bem diferentes em determinadas operações, o que inviabilizava a produção em massa em um layout linear com balanceamento entre as operações da linha de montagem. A variedade dos tempos de processamento implicava diferentes roteiros de produção, tornando o layout funcional mais adequado para a fábrica em questão.
Logo no início do trabalho, procurou-se desenhar o layout atual representando os espaços em blocos (block layout), conforme pode ser observado na planta baixa apresentada na figura 1. Para a realização dessa etapa, foram utilizados os documentos de especificação e as plantas originais de construção da fábrica, sendo que as dimensões foram atualizadas por meio de medições in loco, feitas com o auxílio de uma trena.
Com base na planta baixa atualizada, foram definidas as unidades de planejamento de espaço (UPE's). Para essa definição, foram focalizadas prioritariamente as áreas que interferiam diretamente na transformação de matéria-prima em produtos acabados. Além disso, foi realizado um check-list para verificar os aspectos de infraestrutura (ex.: utilidades, equipamentos de movimentação, etc.) que a fábrica possuía e que poderiam ser necessários no futuro, de forma a dar suporte para a identificação de UPE's. Em complemento, foi feito um levantamento de máquinas e equipamentos relacionados com as operações produtivas, para que se tivesse noção das futuras necessidades de capacidade produtiva. De acordo com esses princípios, foram definidas 18 UPE's situadas na planta baixa da figura 2. Dentre os setores mostrados na planta baixa, somente o escritório e o banheiro não foram considerados como unidades de planejamento de espaço, pois estavam fora do escopo do projeto.
Figura 2. Layout atual.
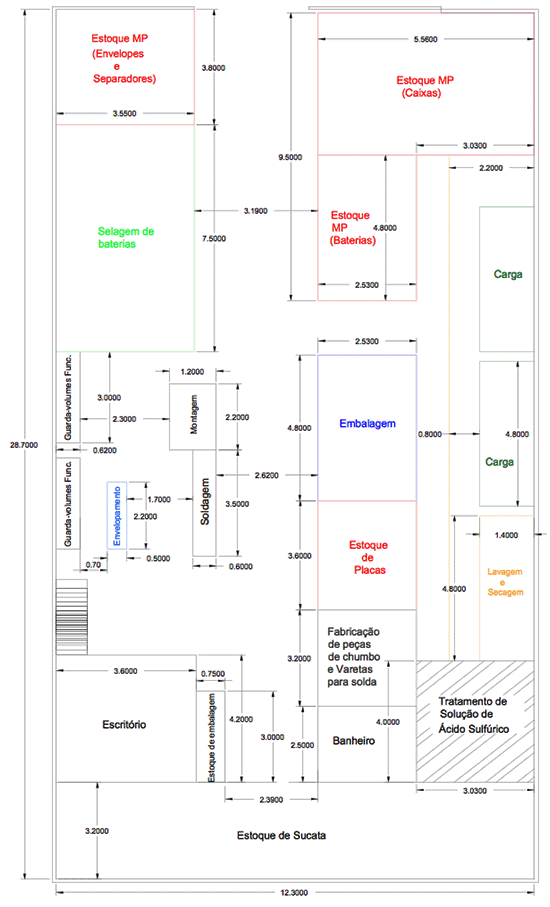
Considerando que a fábrica produzia diferentes tipos de bateria, foi selecionado o produto de maior demanda para a aplicação da análise de fluxos, segunda etapa da metodologia proposta. Com base na maior demanda, foi escolhido o processo de fabricação da bateria de 60 Ah, definida como produto-padrão da análise de fluxos. Para esse processo foram utilizadas três ferramentas de mapeamento: fluxograma em ramos, gráfico de fluxo de processo e mapofluxograma. Conforme apresentam as figuras 3, 4 e 5, as ferramentas se complementaram, uma vez que permitiram visualizar o processo de três perspectivas diferentes. Essas três perspectivas possibilitaram compreender a relação entre a sequência de operações, os tempos produtivos e a localização desses fluxos no chão-de-fábrica.
Figura 3. Fluxograma em ramos para o processo de produção da bateria de 60 Ah.

Figura 4. Gráfico de fluxo para o processo de produção da bateria de 60 Ah.

Figura 5. Mapofluxograma para o processo de produção da bateria de 60 Ah.

A partir da análise de fluxos, procurou-se quantificar o volume de material transportado e o número de movimentações entre as UPE's, tornando possível a construção de cartas "de-para" com essas informações. As cartas "de-para" foram convertidas em matrizes de afinidades, utilizando a escala de 0 a 4, como sugere o método FacPlan.
Na definição das afinidades não relacionadas ao fluxo (critérios qualitativos), observou-se que as razões para atribuir o grau de importância das inter-relações eram todas vinculadas e proporcionais à intensidade do fluxo. Por esse motivo, ao invés de elaborar uma matriz de afinidades não relacionadas ao fluxo, optou-se por combinar as duas matrizes de afinidades relacionadas ao fluxo que haviam sido feitas, baseadas no volume de material transportado e no número de movimentações entre as UPE's. A matriz combinada utilizou a média aritmética das duas matrizes, pois foram atribuídos pesos iguais para ambas. Os resultados da matriz combinada foram arredondados para os números inteiros mais altos (ex.: 1,5 ≈ 2), permitindo que se obtivessem valores de acordo com a escala de 0 a 4 (figura 6). Os valores da matriz combinada foram utilizados para o desenho do diagrama de configurações, apresentado na figura 7 em posição sobreposta ao layout atual.
Figura 6. Matrizes de afinidades entre as UPE's.

Figura 7. Diagrama de configurações situado no layout atual.

Na análise de espaços necessários, identificou-se que os espaços disponíveis já eram suficientes para a execução das operações da fábrica, considerando inclusive o futuro aumento de demanda. Portanto, a simulação das diferentes configurações de layout considerou o dimensionamento atual das instalações, possibilitando o planejamento primitivo do espaço apenas com o intercâmbio entre os blocos que representavam as UPE's.
Algumas alternativas foram geradas, sendo que, para cada uma delas, havia um diagrama de configurações correspondente. Na avaliação de alternativas, procurou-se privilegiar aquelas que aproximavam as UPE's com maiores graus de afinidade. De acordo com as diferentes configurações testadas, foi escolhida a alternativa que é apresentada na figura 8.
Figura 8. Layout proposto.

Ao projetar a alternativa de layout escolhida, optou-se por não fazer modificações de grande porte, uma vez que a fábrica ainda pode ser considerada nova e necessita de um tempo maior para ajustar sua produção ao espaço físico. Dentre as modificações que podem ser percebidas na figura 8, destacam-se:
- O setor de envelopamento de placas foi agregado ao estoque de placas, que resultará em uma diminuição do número de movimentações entre os dois setores e em uma redução do lead time de preparação de placas envelopadas. Com essa mudança, as placas serão processadas no mesmo espaço em que estão armazenadas, melhorando a circulação de materiais e pessoas nas áreas que ficarão livres.
- O estoque de embalagens foi agregado à bancada da operação de embalagem de baterias, evitando as longas movimentações e os cruzamentos de fluxos que ocorrem atualmente. Além disso, essa alteração permite que o controle do estoque de embalagens seja feito pelos próprios operadores do setor de embalagens, fator que influencia positivamente na motivação dos funcionários e na acurácia dos dados de estoque.
Ao escolher uma alternativa de layout que propõe modificações modestas, a empresa levou em consideração a oportunidade de executar alterações de baixo custo, que não impliquem em reformas que obriguem a parar a produção, mas que tragam retornos visíveis em termos de melhoria do fluxo de processo. Isso reflete a intenção da empresa em continuar monitorando o desempenho do layout, implementando melhorias graduais e antecipadas ao longo do tempo, ao invés de deixar que o layout gere problemas que venham necessitar de medidas emergenciais.
5. Considerações finais
Este artigo apresentou a aplicação do planejamento sistemático de layout em uma pequena fábrica de baterias automotivas, reforçando a validade dessa tradicional metodologia para a melhoria de layouts existentes. Essa constatação também foi válida para a aplicação em layouts de pequeno porte, algo que é necessário, porém geralmente negligenciado devido à informalidade comum às pequenas empresas.
Embora a intuição, a experiência e a criatividade sejam ingredientes essenciais no projeto um arranjo físico industrial, é muito importante que o processo de reorganização de layout também siga princípios racionais, facilitado pelo uso de técnicas sistemáticas. A aplicação provou que, mesmo que o layout atual não apresentasse problemas graves, a utilização de técnicas sistemáticas mostrava uma perspectiva diferente para os gerentes da empresa, que passaram a visualizar alternativas de otimização de fluxos para obter vantagens de eficiência em relação à concorrência.
A metodologia que foi utilizada neste trabalho foi derivada dos métodos SLP e FacPlan. Mesmo que esses métodos já apresentem roteiros suficientemente claros para serem seguidos, a aplicação relatada neste artigo chama a atenção para a importância do senso crítico e da necessidade de adequar metodologias genéricas às características específicas dos layouts analisados e de seus respectivos sistemas de produção. Nesse sentido, este trabalho contribui com uma metodologia que foi simplificada a um caso particular, mas que certamente encontra situações paralelas na indústria, especialmente em fábricas de pequeno porte que operam em layouts funcionais. Portanto, apesar da cautela que se deve ter com a generalização de apenas uma aplicação, pode-se afirmar que a metodologia certamente traria benefícios para layouts semelhantes.
A continuidade desse trabalho se apresenta na empresa com o monitoramento e a melhoria gradual do layout por meio da utilização da metodologia proposta. Isso implica a definição de indicadores de desempenho relacionados ao layout, de maneira que a necessidade de novas instalações se apresente antes de sua obsolescência. Além disso, deve-se ter consciência de que a metodologia é dinâmica, sendo que, a cada alteração significativa na demanda e a cada introdução de um novo produto, os fluxos devem ser analisados novamente e as configurações alternativas de layout devem ser reavaliadas.
Em âmbito acadêmico, sugere-se a continuidade da pesquisa por meio do incremento da metodologia com técnicas mais sofisticadas de apoio à decisão, como por exemplo, a simulação computacional das diferentes alternativas de layout. A partir da simulação computacional, seria muito mais fácil prever modificações sem que fosse necessário um estudo completo de layout a cada alteração no sistema produtivo.
Referências
Chien, T. (2004); "An empirical study of facility layout using a modified SLP procedure", Journal of Manufacturing Technology Management, 15(6), 455-465.
Coughlan, P.; Coghlan, D. (2002); "Action research for operations management", International Journal of Operations & Production Management, 22(2), 220-240.
Djassemi, M. (2007); "Improving factory layout under a mixed floor and overhead material handling condition", Journal of Manufacturing Technology Management, 18(3), 281-291.
Eden, C.; Huxham, C. (1996); "Action research for management research", British Journal of Management, 7(1), 75-86.
Garcia-Diaz, A.; Smith, J. M. (2008); Facilities planning and design, Prentice Hall, Upper Saddle River.
Heizer, J.; Render, B. (2001); Administração de operações: bens e serviços, 5 ed., LTC, Rio de Janeiro.
Kerns, F. (1999); "Strategic facility planning (SFP)", Work Study, 48(5), 176-181.
Lee, Q. (1998); Projeto de instalações e do local de trabalho, IMAM, São Paulo.
Marujo, L. G.; Carvalho, D.; Leitão, M. N. (2010); "Otimização de layout utilizando-se o SLP combinado com teoria das filas: um estudo de caso em uma oficina de rodas e freios de aeronaves", Revista Gestão Industrial, 6(4), 93-109.
Muther, R. (1978); Planejamento do layout: sistema SLP, Edgard Blücher, São Paulo.
Muther, R.; Wheeler, J. D. (2000); Planejamento simplificado de layout: sistema SLP, IMAM, São Paulo.
Tompkins, J. A.; White, J. A.; Bozer, Y. A.; Tanchoco, J. M. A. (2010); Facilities planning, 4 ed., John Wiley & Sons, New York.
Tortorella, G. L.; Fogliatto, F. S. (2008); "Planejamento sistemático de layout com apoio de análise de decisão multicritério", Produção, 18(3), 609-624.
Villar, A. M.; Nóbrega Júnior, C. L. (2004); Planejamento das instalações industriais, Manufatura, João Pessoa.
Yang, T.; Su, C.; Hsu, Y. (2000); "Systematic layout planning: a study on semiconductor wafer fabrication facilities", International Journal of Operations & Production Management, 20(11), 1359-1371. |