1. Introdução
Durante muito tempo o setor industrial, em geral, desenvolveu suas atividades de produção de bens sem a preocupação com a redução da quantidade de resíduos. Com o surgimento de políticas nacionais voltadas a conservação do meio ambiente, passa a existir a consciência que a geração de novos produtos através da reciclagem de resíduos é uma alternativa concreta, já que o desenvolvimento sustentável requer uma redução do consumo de matérias-primas não renováveis.
Segundo a Comissão Mundial sobre Meio Ambiente e Desenvolvimento (Comissão Brundtland) desenvolvimento sustentável é o desenvolvimento que satisfaz as necessidades do presente sem comprometer a capacidade das gerações futuras satisfazerem as suas próprias, ou é, significa melhorar a qualidade da vida humana, sem exceder a capacidade de suporte que sustenta os ecossistemas. O tema desenvolvimento sustentável está presente em vários trabalhos e pode-se destcar Vinãs, Pérez e Gonzáles (1998), Cruces H. (1997) e Figueiredo, Prodanov e Pedde (2010).
A indústria metalúrgica é uma grande geradora de resíduos e consumidora de matérias-primas. Os resíduos de fundição areia descartada de fundição, o cavaco de usinagem, a lama de tratamento da água de refrigeração, a escória de fundição e o pó de exaustão são alguns dos resíduos gerados durante o processo. Neste ambiente é possível perceber que o desenvolvimento de tecnologias ambientalmente eficazes e seguras para que o retorno destes resíduos a cadeia produtiva é extremamente importante.
O emprego de resíduos de fundição em concretos e argamassas contribui com a sustentabilidade ao evitar-se o impacto ambiental causado pelo descarte no meio ambiente. Os estudos sobre concreto e argamassa sustentáveis incluem aqueles que se dispõe a consumir rejeitos industriais. Os rejeitos da indústria metalúrgica podem ser incorporados em materiais cimentícios de forma geral.
Neste contexto este trabalho tem por objetivo propor a incorporação do resíduo pó de exaustão de fundição em argamassas para assentamento e revestimento de paredes e tetos como alternativa para o desenvolvimento sustentável. Segundo Rocha e John (2003), a importância do aproveitamento de resíduos na construção civil deve-se basicamente a possibilidade de desenvolvimento de materiais de baixo custo a partir de resíduos industriais, disponíveis localmente, através da investigação de suas potencialidades e ao uso de materiais e processos que causem mínimo impacto na cadeia produtiva.
O artigo está estruturado da seguinte forma: (1) Introdução; (2) Geração e Utilização de Areia e Pó de Exaustão (Revisão bibliográfica sobre o tema); (3) Metodologia de Pesquisa; (4) Análise e Discussão dos Resultados e finalmente (5) Considerações Finais e Referências.
2. Geração e Utilização de Areia e Pó de Fundição
Estima-se que a quantidade de areia nova utilizada pelas indústrias de fundição no Brasil está em torno de três milhões de toneladas ao ano e gera igual quantidade de resíduo (ABIFA, 2009). O descarte destes resíduos traz diversos danos ao meio ambiente como modificação da paisagem natural e ocupação de grandes áreas com a disposição em aterros.
As areias residuais de uma fundição, de forma geral, podem ser classificadas como areia de processo e areia de macharia. A areia de processo é também conhecida como areia verde e a areia de macharia é ligada com o auxílio de resinas. O funcionamento de um sistema de areia de fundição é mostrado esquematicamente na figura 1, onde são apresentados os procedimentos envolvidos na recuperação e no recondicionamento de uma areia do sistema, bem como, os elementos que entram e saem do sistema a cada ciclo.
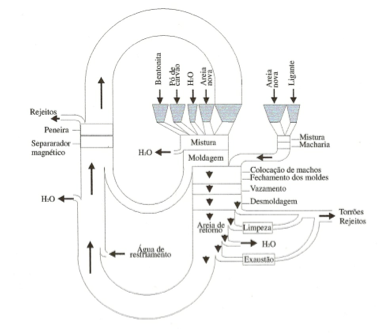
Figura 1 - Funcionamento de um sistema de areia de fundição (MARIOTTO, 2000).
O pó de exaustão, resíduo de fundição utilizado neste trabalho, é gerado a partir da mistura de areia de sílica e outros aditivos utilizados na fabricação de machos para a produção de peças metálicas nas indústrias de fundição. Por motivos diversos, alguns machos são refugados durante o processo de fabricação. Estes machos refugados são enviados para o processo de regeneração de areias de macharia. O pó de exaustão é separado da areia regenerada proveniente do sistema de regeneração por meio de captação por filtros manga em pontos distintos durante o processo, pois a areia regenerada deve atender as especificações de granulometria de uso para a confecção de machos e a escolha deste granulometria depende do acabamento desejado da peça. Quando maior o módulo de finura melhor o acabamento, maior o consumo de resina, menor permeabilidade, menor colapsibilidade (CORREIA, 2003). O pó de exaustão, material fino originado das areias de macharia é um resíduo de fundição que pode ser incorporado em materiais cimentícios.
Existem vários estudos sobre materiais cimentícios sustentáveis, ou seja, com incorporação de resíduos industriais. A seguir, para complementar a revisão bibliográfica, são relatadas várias pesquisas que tratam de temas relacionados à utilização de resíduos de fundição em argamassas e concretos.
A análise das propriedades de materiais cimentícios com incorporação de pó de fundição é investigada nas pesquisas de Kraus et al (2009) onde são apresentados resultados experimentais sobre o uso de pó de fundição contendo sílica em concreto. Foram observados mudanças na cor do concreto e também na sua viscosidade. A incorporação de pó de fundição produz um concreto mais econômico. Santos et al (2010) relatam o uso de pó de exaustão de fundição em substituição parcial a areia natural no concreto convencional. A resistência mecânica de compressão do concreto com a substituição de 15% do agregado miúdo pelo pó de exaustão ficou próxima dos valores encontrados sem a utilização do mesmo. Analisando os resultados através da análise de experimentos, verificou-se que é viável a substituição do pó de exaustão nas proporções em até 15%. Pereira et al (2011) analisam a retenção de água em argamassas para revestimento de teto e paredes através do uso de delineamento de misturas. A superfície de resposta gerada mostrou que a capacidade de retenção de água das argamassas pode ser classificada como normal e alta. Em relação à retenção de água, a incorporação do resíduo pó de exaustão de fundição nas proporções estudadas de 5%, 10% e 15% é viável nestes tipos de argamassas.
A incorporação de areia de fundição em substituição parcial a areia natural é analisada nos trabalhos de Monosi, Sani e Tittarelli (2010). Foi observado que a trabalhabilidade das argamassas não foi alterada se a substituição for de até 10%. Em dosagens maiores é necessária a adição de plastificantes para obtenção da mesma trabalhabilidade. Também foi observado uma diminuição da resistência mecânica em torno de 20% até 30%. Guney et al (2010) investigam a utilização de areia de fundição em substituição parcial da areia natural fina nas proporções de 0%, 5%, 10% e 15% em concreto. Foi observado que o concreto contendo até 10% de areia de fundição apresentou resultados de resistência à compressão e tração e módulo de elasticidade semelhantes ao concreto sem areia de fundição. Khatib, Herki e Kenai (2013) investigam as propriedades do concreto com areia de fundição. O agregado fino natural foi substituído em peso em porcentagens de 0%, 30%, 60% e 100%. As propriedades estudadas foram absorção de água e resistência à compressão. Os resultados indicam que há um aumento na absorção de água e uma diminuição na resistência à compressão em relação ao aumento da quantidade de areia de fundição na mistura.
Siddique e Singh (2011) apresentam uma visão geral de algumas das pesquisas publicadas sobre o uso de areia de fundição em concreto. Os efeitos do uso da areia de fundição em propriedades como resistência a compressão, resistência à tração, resistência ao congelamento e módulo de elasticidade são apresentados. Em outras pesquisas Singh e Siddique (2012) descrevem os efeitos da utilização da areia de fundição em substituição parcial ao agregado miúdo sobre a resistência e permeabilidade do concreto. Foram feitas substituições em peso de 0%, 5%, 10%, 15% e 20% e foi verificado aumento de resistência e permeabilidade. Os mesmos autores Singh e Siddique (2012) em outro trabalho analisam a resistência à abrasão e outras propriedades de resistência do concreto com areia de fundição em proporções de substituição em relação ao agregado natural variadas. As propriedades analisadas foram resistência à compressão, resistência à tração, resistência à abrasão e módulo de elasticidade. Os resultados mostram uma melhoria contínua destas propriedades com a substituição parcial dos agregados por areia de fundição.
A adição de areia de fundição e outros componentes em concreto é relatada em pesquisas. Siddique e Kadri (2011) relatam o efeito da substituição parcial do cimento por metacaulim na permeabilidade e absorção de água do concreto onde 20% dos agregados é areia de fundição. Os resultados mostraram que a adição de metaucaulim faz a permeabilidade do concreto aumentar. Sahmaran et al (2011) analisam o uso de areia de fundição e cinzas volantes em concreto. Foi verificado que a substituição de 100% do agregado miúdo por areia de fundição e 70% de aglomerante por cimento com cinzas volantes tornou o concreto de baixo custo.
O efeito da adição de fungos em concretos produzidos com areia de fundição é analisada através dos trabalhos de Kaur, Siddique e Rajor (2012). Os autores investigam o efeito da incorporação de fungos (Aspergillus spp.) tratados em concretos que utilizam areia de fundição como agregado na proporção de 20%. O Aspergillus spp. aumenta a capacidade do cimento reagir adequadamente na presença do resíduo de fundição. O estudo evidenciou um aumento na resistência à compressão à 28 dias, diminuição de porosidade e absorção de água. Em outra pesquisa, Kaur, Siddique e Rajor (2013) apresentam uma análise da microestrutura do concreto com adição de areia de fundição em diferentes porcentagens (0%, 10%, 15% e 20% em massa) e fungos (Aspergillus niger). As análises confirmam a melhoria das propriedades do concreto devido a formação de cálcio nos poros do material.
3. Metodologia de pesquisa
A abordagem metodológica dessa pesquisa é exploratória e experimental. A pesquisa foi estruturada em duas etapas. A primeira etapa envolveu uma revisão bibliográfica sobre tema. Na segunda etapa foi realizado um estudo experimental para verificar a adequação ao uso da argamassa com incorporação de pó de exaustão de fundição em relação às propriedades de resistência à tração na flexão e à compressão segundo a NBR 13279 (ABNT, 2005).
3.1 Materiais utilizados
Para preparar as misturas de argamassa para assentamento e revestimento de paredes e tetos foram utilizados aglomerantes (cimento e cal), agregado miúdo (areia fina) e água proveniente do sistema de abastecimento da rede pública de Joinville - SC no Brasil. O cimento CP II E-32 tem adição de escória granulada de alto-forno e combina com bons resultados o baixo calor de hidratação com o aumento de resistência do cimento Portland comum. Este cimento serve para diversas aplicações como a produção de argamassa e tem resistência à compressão aos 28 dias de 32 MPa. A Tabela 1 traz a composição química do cimento CP II E-32.
Tabela 1 – Valores da composição de compostos do cimento Portland CP II E-32
Composição de compostos (%) |
C3A |
C2S |
C3A |
C4AF |
CaSO4 |
CaO livre |
MgO |
Perda ao fogo |
46 |
29 |
6 |
12 |
2,8 |
0,6 |
3,0 |
1,0 |
A cal hidratada CH-III é produzida através da calcinação da pedra calcária dolomítica e é constituída essencialmente de uma mistura de hidróxido de cálcio, hidróxido de magnésio e óxido de magnésio, com teor de gás carbônico igual ou menor que 13%. A cal hidratada proporciona boa plasticidade às argamassas.
O agregado miúdo utilizado na produção das argamassas é comercializado como areia comum em sacos de 20 Kg. Esta areia foi caracterizada em relação à distribuição granulométrica, massa unitária no estado solto, massa específica real, impurezas orgânicas e teor de material pulverulento segundo as normas técnicas brasileiras NBR NM 248 (ABNT, 2003), NBR 7251 (ABNT, 1982), NBR NM 52 (ABNT, 2009), NBR NM 49 (ABNT, 2001) e NBR NM 46 (ABNT, 2003). O pó de exaustão, resíduo proveniente da indústria metalúrgica Fundição Tupy - S.A, situada em Joinville-SC no Brasil foi caracterizado em relação à distribuição do tamanho de partícula por difração a laser e também foi realizada análise química.
3.2 Delineamento por misturas
No procedimento experimental foi utilizado planejamento de experimentos delineamento de misturas com o objetivo de alcançar eficiência no procedimento experimental. O delineamento experimental de misturas é problema que envolve metodologia de superfície de resposta. Neste caso, as condições de processo são mantidas constantes e os fatores são componentes ou ingredientes de uma mistura, e a resposta depende das frações dos ingredientes presentes (MONTGOMERY, 2003).
A composição de uma mistura pode ser considerada em termos das frações dos componentes, em uma representação geométrica. No caso de misturas com três componentes a figura é um triângulo com lados iguais. As diferentes composições possíveis são representadas pelos pontos pertencentes ao triângulo. Os vértices correspondem aos componentes puros e os lados às misturas binárias, enquanto os pontos situados no interior do triângulo representam as possíveis misturas para os três componentes. Na maioria dos experimentos com misturas existem restrições em relação à quantidade dos materiais constituintes utilizados por motivos tecnológicos ou econômicos.
Foram fixados valores mínimos e máximos de quantidades para os materiais constituintes das argamassas baseados em traços pré-fixados utilizados em argamassa de assentamento e revestimento de paredes e tetos. Os aglomerantes cal e cimento foram usados em proporções iguais em massa. A composição da dez misturas de argamassas foi gerada pelo programa estatístico STATISTICA 7.1 (StatSoft Inc.,2006) que traz o planejamento de experimentos delineamento de misturas entre o seus módulos. A Tabela 2 mostra a composição das argamassas em massa obtida pelo programa.
Tabela 2 – Composição em massa das argamassas
Mistura |
Aglomerantes (cimento e cal)
% em massa |
Areia
% em massa |
Resíduo
% em massa |
1 |
30,00 |
65,00 |
05,00 |
2 |
20,00 |
75,00 |
05,00 |
3 |
20,00 |
65,00 |
15,00 |
4 |
25,00 |
70,00 |
05,00 |
5 |
25,00 |
65,00 |
10,00 |
6 |
20,00 |
70,00 |
10,00 |
7 |
23,33 |
68,33 |
08,33 |
8 |
26,67 |
66,67 |
06,67 |
9 |
21,67 |
71,67 |
06,67 |
10 |
21,67 |
66,67 |
11,67 |
3.3 Procedimento de mistura, moldagem e determinação da resistência
O preparo da mistura e a determinação do índice de consistência seguiu o procedimento descrito da norma brasileira NBR 13276 (ABNT, 2005). Cada mistura de argamassa de cal hidratada foi preparada com antecedência de 24 horas. Durante 4 minutos foi misturada em velocidade baixa no recipiente do misturador mecânico (Figura 2a), areia e cal hidratada nas quantidades definidas pelo planejamento de experimentos e água. A quantidade de água de amassamento foi fixada com o objetivo de gerar argamassas trabalháveis para todas as misturas definidas no delineamento por misturas. A argamassa foi pesada para posterior acréscimo de água correspondente a perda por evaporação. Após o intervalo o cimento foi acrescentado na mistura que foi homogeneizada por 4 minutos no recipiente do misturador em velocidade baixa.
Após a preparação da argamassa foi realizado o ensaio para a determinação do índice de consistência. Foi preenchido um molde tronco-cônico com argamassa fresca e após a retirada do molde foi efetuado 30 golpes da mesa de consistência com acionamento elétrico (Figura 2b).
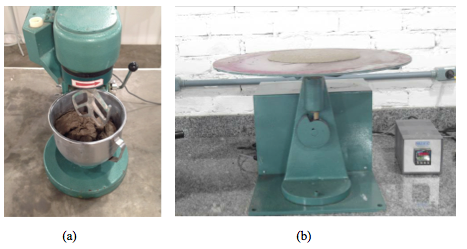
Figura 2 – (a) Misturador mecânico e (b) mesa de consistência
Imediatamente após a última queda da mesa foi medido com o auxílio do paquímetro o espalhamento do molde tronco-cônico original de argamassa.
Após o preparo da argamassa com o molde fixo à mesa de adensamento foi introduzido duas camadas de argamassa e após cada camada foi aplicado 30 quedas na mesa de adensamento. Foram preparados 30 corpos-de-prova para o ensaio de resistência à compressão e resistência à tração na flexão. Todos os corpos-de-prova foram moldados em formas prismáticas metálicas 4cmx4cmx16cm (Figura 3a). Os corpos-de-prova foram desmoldados 48 horas após a moldagem e a cura aconteceu ao ar livre (Figura 3b).

Figura 3 – (a) Moldes prismáticos metálicos preenchidos com argamassa e (b) corpos-de-prova desmoldados
A determinação da resistência à tração na flexão e à compressão seguiu as indicações da norma brasileira NBR 13279 (ABNT, 2005). Para a determinação da resistência à tração na flexão, o corpo-de-prova foi posicionado no dispositivo de apoio (Figura 4a) e posteriormente foi aplicada uma carga de (50±10)N/s até a ruptura na máquina universal de ensaios modelo DL 10000 da marca EMIC. Na determinação da resistência à compressão foram utilizadas as metades dos corpos-de prova do ensaio de flexão (Figura 4b) e a carga aplicada foi de (500±50)N/s até a ruptura na máquina da EMIC modelo PC 200.

Figura 4 – Dispositivo de apoio para o ensaio de resistência à tração na flexão (a) e de resistência à compressão (b)
4. Análise e Discussão dos Resultados
4.1 Agregado miúdo e pó de exaustão
O agregado miúdo utilizado na produção das argamassas pode ser classificado como uma areia fina, com diâmetro máximo característico 2,36 mm e módulo de finura 2,32. A Figura 5 mostra as características visuais da areia.
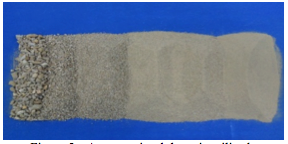
Figura 5 – Aspecto visual da areia utilizada
A curva granulométrica (Figura 6) do agregado miúdo apresenta a característica de um “S” suave que indica uma granulometria contínua.
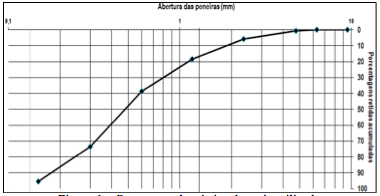
Figura 6 – Curva granulométrica da areia utilizada
A massa específica real da areia foi de 2,62g/cm3 e a massa unitária no estado solto foi de 1,38g/cm3, valores convencionais de massa de areia natural. O teor de materiais pulverulentos ficou em 3,5% e a quantidade de impurezas orgânicas foi de 300ppm. Estes valores estão dentro dos admissíveis por norma.
O pó de exaustão, resíduo utilizado na produção das argamassas, é proveniente do sistema de regeneração das areias de macharia da indústria Fundição Tupy situada no munícipio de Joinville-SC no Brasil. A Figura 7 mostra o aspecto visual do pó de exaustão.
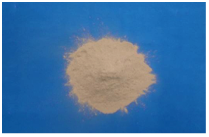
Figura 7 – Aspecto visual do pó de exaustão de fundição
A distribuição granulométrica do pó de exaustão pode ser observada na Tabela 3. O material apresenta grande quantidade de partículas consideradas pulverulentas. Os materiais pulverulentos quando presentes em grande quantidade na argamassa aumentam a exigência de água para a obtenção da mesma consistência.
Tabela 3 – Distribuição do tamanho de partículas do pó de exaustão (SANTOS, 2010)
Distribuição de tamanho das partículas |
10% abaixo de |
50% abaixo de |
90% abaixo de |
100% abaixo de |
Tamanho (µm) |
4,89 |
37,45 |
88,19 |
180,00 |
Em relação à análise química, os valores encontrados em relação aos elementos presentes podem ser observados na Tabela 4.
Tabela 4 – Análise química e absorção do pó de exaustão (SANTOS, 2010)
Elemento |
Al2O3 |
CaO |
Fe2O3 |
K2O |
MgO |
MnO |
Na2O |
P2O5 |
SiO2 |
TiO2 |
Teor (%) |
9,33 |
0,25 |
4,01 |
1,57 |
0,40 |
0,05 |
0,25 |
0,04 |
80,73 |
0,39 |
Perda ao Fogo (%) |
|
|
|
|
|
|
|
2,37 |
4.2. Resistência à tração na flexão e à compressão aos 28 dias e análise estatística
As argamassas destinadas ao assentamento e revestimento de paredes e tetos no Brasil devem cumprir os requisitos estabelecidos na NBR 13281 (2005), sendo classificadas conforme as propriedades e características que apresentam. O índice de consistência das argamassas resultantes das dez misturas ficou em 255±10mm, representando uma consistência adequada ao uso sendo citada em trabalhos científicos como o de Correia et al (2009). A Tabela 5 mostra os resultados encontrados para a resistência à tração na flexão e à compressão aos 28 dias e a classificação das argamassas.
Tabela 5 – Valores da resistência à tração na flexão e à compressão aos 28 dias e classificação das misturas
Mistura |
Aglomerantes (% em massa) |
Areia
(% em massa) |
Resíduo
(% em massa) |
Resistência à tração na flexão aos 28 dias
(MPa) |
Resistência à compressão aos 28 dias
(MPa) |
Classificação
(NBR 13281) |
1 |
30,00 |
65,00 |
05,00 |
2,38±0,30 |
11,44±0,05 |
R4, P6 |
2 |
20,00 |
75,00 |
05,00 |
1,19±0,04 |
5,00±0,10 |
R2, P4 |
3 |
20,00 |
65,00 |
15,00 |
1,35±0,14 |
4,82±0,14 |
R2, P4 |
4 |
25,00 |
70,00 |
05,00 |
1,73±0,03 |
10,59±0,12 |
R3, P6 |
5 |
25,00 |
65,00 |
10,00 |
1,83±0,22 |
7,71±0,21 |
R4, P5 |
6 |
20,00 |
70,00 |
10,00 |
1,21±0,09 |
5,86±0,03 |
R2, P4 |
7 |
23,33 |
68,33 |
08,33 |
1,65±0,06 |
7,47±0,12 |
R3, P5 |
8 |
26,67 |
66,67 |
06,67 |
2,00±0,06 |
10,04±0,24 |
R4, P6 |
9 |
21,67 |
71,67 |
06,67 |
1,35±0,07 |
6,54±0,24 |
R2, P5 |
10 |
21,67 |
66,67 |
11,67 |
1,37±0,11 |
5,38±0,16 |
R2, P5 |
Os dados referentes à resistência à tração na flexão foram analisados pelo programa estatístico STATISTICA 7.1 (StatSoft Inc.,2006) admitindo um nível de significância de 0,05. No módulo de análise do delineamento por misturas foi selecionado um modelo quadrático (Equação 1) para a modelagem da resistência à tração na flexão pois foi o modelo que melhor se ajustou aos dados experimentais de acordo com as definições de Montgomery (2003). Usando a abordagem de teste das hipóteses, ou seja, o valor de p deve ser menor ou igual ao nível de significância, o modelo apresentou p = 0,0013. A variabilidade dos dados, explicada pela análise de variância é relativamente reduzida apresentado valor de R2=0,9824.
TF (MPa) = +2,40X + 1,20Y + 1,37Z - 0,15XY - 0,21XZ - 0,21YZ (Equação 1)
Onde:
- TF-Resistência à tração na flexão aos 28 dias
- X-Aglomerante (cimento + cal em proporções iguais em massa)
- Y-Areia
- Z-Resíduo
Posteriormente os dados referentes à resistência à compressão foram novamente analisados pelo programa estatístico STATISTICA 7.1 (StatSoft Inc.,2006) admitindo o mesmo nível de significância de 0,05 da análise anterior. O modelo escolhido foi o quadrático (Equação 2) para a modelagem da resistência à compressão pois foi o modelo que melhor se ajustou aos dados provenientes dos estudos práticos. Os valores de p = 0,0011 e R2=0,9840 foram encontrados para este modelo e estão de acordo com as definições estatísticas.
Os valores estatísticos de p e R2 encontrados para a modelagem da resistência à tração na flexão e à compressão são semelhantes aos valores encontrados em outros trabalhos de análises estatísticas e modelagem de propriedades por planejamento de experimentos como Correia et al (2010), Senft et al (2009) e Chen et al (2010).
C (MPa) = +11,71X + 4,73Y + 4,97Z + 8,61XY – 3,72XZ + 1,52YZ (Equação 2)
Onde:
- C-Resistência à compresão aos 28 dias em MPa
- X-Aglomerante (cimento + cal em proporções iguais em massa) em % de massa
- Y-Areia em % de massa
- Z-Resíduo em % de massa
Os valores encontrados para a resistência à tração na flexão e à compressão aos 28 dias podem ser observados em gráficos triangulares de curvas de nível. Nos gráficos abaixo (Figura 8 e 9) pode-se observar a tendência dos maiores valores de resistência à tração na flexão e à compressão aos 28 dias estarem relacionados às misturas com as maiores quantidades de aglomerantes. Em relação às propriedades de resistência à tração na flexão e à compressão, as misturas apresentam os requisitos exigíveis para argamassa de assentamento e revestimento de paredes e tetos conforme a NBR 13281 (2005), tornando viável a utilização das misturas estudadas.
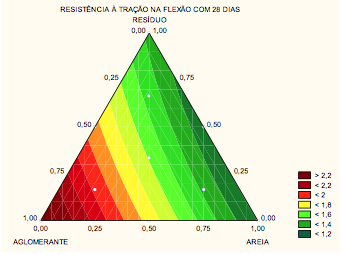
Figura 8 – Gráfico de curvas de nível da resistência à tração na flexão aos 28 dias
-----

Figura 9 – Gráfico de curvas de nível da resistência à compressão aos 28 dias
Na análise estatística foi considerado que os dados obtidos no procedimento experimental têm comportamento normal. Então a validade do modelo adotado pode ser comprovada pelo gráfico de probabilidade normal dos resíduos para o experimento que determina a resistência à tração na flexão e à compressão aos 28 dias (Figura 10 e 11). Os valores plotados bem próximo a reta indicam um comportamento normal dos dados obtidos.

Figura 10 - Gráfico de probabilidade normal dos resíduos para o modelo de análise da resistência à tração na flexão aos 28 dias
-----

Figura 11 - Gráfico de probabilidade normal dos resíduos para o modelo de análise da resistência à compressão aos 28 dias
5. Considerações Finais
As modelagens das propriedades resistência à tração na flexão e à compressão aos 28 dias usando planejamento de experimentos delineamento por misturas podem ser utilizadas como diretrizes em estudos de argamassas com incorporação de resíduos de fundição. A comparação dos resultados obtidos pelas equações dos modelos estatísticos com os resultados experimentais encontrados para as propriedades investigadas mostram um erro relativamente baixo, o que valida os modelos encontrados. Foi verificado que a proporção entre aglomerantes e agregados na mistura de argamassa influencia diretamente na propriedade da resistência à tração na flexão e à compressão aos 28 dias.
Quanto aos trabalhos futuros sugere-se o estudo da influência da incorporação do resíduo pó de exaustão de fundição em relação a outras propriedades relevantes para argamassas como retenção de água e resistência de aderência à tração.
Diante da proposta e dos resultados encontrados, a incorporação de pó de exaustão de fundição em argamassas de assentamento e revestimento de paredes e tetos em relação às propriedades estudadas não é apenas uma solução viável, mas também uma alternativa para o descarte de resíduos de fundição no meio ambiente, contribuindo desta forma para o desenvolvimento sustentável.
6. Referências
Associação Brasileira de Fundição – ABIFA (2009); Manual de regeneração e reuso de areias de fundição; São Paulo.
Associação Brasileira de Normas Técnicas – ABNT (1982); NBR 7251: Agregado em estado solto – Determinação da massa unitária. Rio de Janeiro.
Associação Brasileira de Normas Técnicas – ABNT (2001); NBR NM 49: Agregado fino – Determinação de impurezas orgânicas. Rio de Janeiro.
Associação Brasileira de Normas Técnicas – ABNT (2003); NBR NM 248:2003: Agregados – Determinação da composição granulométrica. Rio de Janeiro.
Associação Brasileira de Normas Técnicas – ABNT (2003); NBR NM 46: Agregados – Determinação do material fino que passa através da peneira 75 µm, por lavagem. Rio de Janeiro.
Associação Brasileira de Normas Técnicas – ABNT (2005); NBR 13276: Argamassa para assentamento e revestimento de paredes e tetos – Preparo da mistura e determinação do índice de consistência. Rio de Janeiro.
Associação Brasileira de Normas Técnicas – ABNT (2005); NBR 13279: Argamassa para assentamento e revestimento de paredes e tetos – Determinação da resistência à tração na flexão e à compressão. Rio de Janeiro.
Associação Brasileira de Normas Técnicas – ABNT (2005); NBR 13281: Argamassa para assentamento e revestimento de paredes e tetos – Requisitos. Rio de Janeiro.
Associação Brasileira de Normas Técnicas – ABNT (2009); NBR NM 52: Agregado miúdo – Determinação da massa específica e massa específica aparente. Rio de Janeiro.
Correia, C. J. (2003); Cold-box para Alumínio e Ferro. Congresso de Areia de Fundição, São Paulo.
Correia, S. L.; Partala, T.; Loch, F.; Segadães, A, M. (2010) “Factorial design used to model the compressive strength of mortars containing recycled rubber”, Composite Structures, 92, 2047-2051.
Cruces H., J. M. (1997); “Etapas del discurso ambiental en el tema del desarrollo”, Espacios, 18 (1).
Figueiredo J. A. S.; Prodanov, C. C., Pedde; V. (2010); “La crisis conceptual del “Desarrollo Sostenible”, Espacios, 31 (4), 32.
Guney, Y.; Sari, Y. D.; Yalcin, M.; Tuncan, A.; Donmez, S. (2010); “Re-usage of waste foundry sand in high-strength concrete”, Waste Management, 30, 1705-1713.
Kaur, G.; Siddique, R.; Rajor, A. (2012); “Properties of concrete containing fungal treated waste foundry sand”, Construction And Building Materials, 29, 82-87.
Kaur, G.; Siddique, R.; Rajor, A. (2013); “Micro-structural and metal leachate analysis of concrete made with fungal treated waste foundry sand”, Construction and Building Materials, 38, 94-100.
Khatib, J. M.; Herki, B. A.; Kenai, S. (2013); “Capillarity of concrete incorporating waste foundry sand”, Construction and Building Materials, 47, 867-871.
Kraus, R.N.; Naik, T.R.; Ramme, B.W.; Kumar, R. (2009); “Use of foundry silica-dust in manufacturing economical self-consolidating concrete”, Construction And Building Materials, 23, 3439-3442.
Mariotto, C. L. (2000); Regeneração de areias: uma tentativa de discussão sistemática; São Paulo, Caderno Técnico Fundição e Matérias-Primas, p. A-T.
Monosi, S.; Sani, D.; Tittarelli, F. (2010); “Used Foundry Sand in Cement Mortars and Concrete Production”, The Open Waste Management Journal, 3, 18-25.
Montgomery, D. C.; Runger, G. C. (2003); Estatística aplicada e probabilidade para engenheiros. Rio de Janeiro, LTC.
Pereira, H. R. S.; Valentina, L. V. O. D.; Santos, C. C.; Warsch, P. (2011); Uso de Delineamento de Misturas para Análise da Retenção de Água em Argamassas com Pó de Exaustão de Fundição. 53º Congresso Brasileiro de Concreto, Florianopólis.
Rocha, J. C.; John, V. M. (2003); Utilização de Resíduos na Construção Habitacional; Porto Alegre, Coletânea Habitare, v. 4, 273 p.
Rongzhi C.; Zhenya Z.; Chuanping F.; Ke H; Miao L.; Yuan L.; Kazuya S.; Nan C.; Norio S. (2010); “Application of simplex-centroid mixture design in developing and optimizing ceramic adsorbent for As(V) removal from water solution”, Microporous and Mesoporous Materials, 131, 115-121.
Sahmaran, M.; Lachemi, M.; Erdem, T. e Yücel, H. E. (2011); “Use of spent foundry sand and fly ash for the development of green self-consolidating concrete”, Materials and Structures, 44, 1193–1204.
Santos, C. C. D.; Valentina, L. V. O. D.; Semptikovski, S. C.; Galuppo, W. C. (2010); Uso de Pó de Exaustão de Fundição em Substituição Parcial a Areia Natural no Concreto Convencional. 52º Congresso Brasileiro de Concreto, Porto de Galinhas.
Senff, L.; Barbetta, P.; Repette, W.; Hotza, D.; Paiva, H.; Ferreira, V. M.; Labrincha. J. A. (2009); “Mortar composition defined according to rheometer and flow table tests using factorial designed experiments”, Construction and Building Materials, 23, 3107-3111.
Siddique, R.; Kadri, E. (2011); “Effect ofmetakaolin and foundry sand on the near surface characteristics of concrete”, Construction And Building Materials, 25, 3257-3266.
Siddique, R.; Singh, G. (2011); “Utilization of waste foundry sand (WFS) in concrete manufacturing”, Resources, Conservation And Recycling, 55, 885-892.
Singh, G.; Siddique, R. (2012); “Abrasion resistance and strength properties of concrete containing waste”, Construction And Building Materials, 28, 421-426.
Singh, G.; Siddique, R. (2012); “Effect of waste foundry sand (WFS) as partial replacement of sand on the strength, ultrasonic pulse velocity and permeability of concrete”, Construction and Building Materials, 26, 416-422.
Vinãs, B. C. B.; Pérez G. H., González, A, A. (1998); “Gestión tecnológica y desarrollo sostenible y solidario en los países latinoamericanos: experiencia cubana”, Espacios, 19 (2).
|